An oven is a device which is used to heat treat items, condition metals, and cure metal coatings at high temperatures. Continuous and batch industrial ovens are the two primary types. Batch industrial ovens, as the name implies, handle a large number of items at the same time. Continuous industrial ovens are typically used in large manufacturing and have heating and cooling capabilities. The efficiency of industrial oven can be determined by how they are used. The ovens that use gas, electricity, steam, hot water, microwaves, or fuel oil batch or conveyor loading.
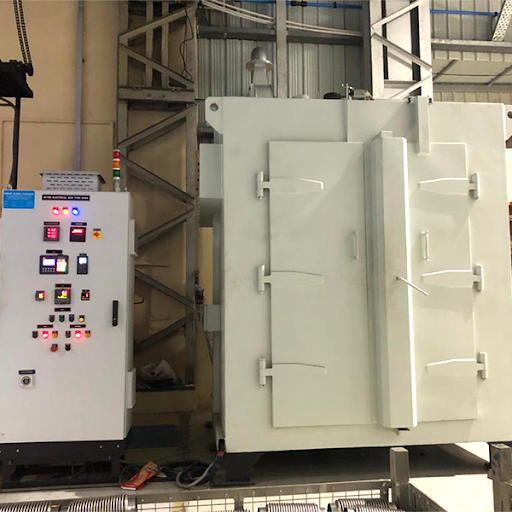
Product loading and airflow patterns are vital to an industrial oven’s success. The six types of airflow differ depending on the product and how it’s loaded. The structure, product handling, and adaptability of the two types of these ovens are all distinct. They’re as follows:
- Ovens for research
Laboratory ovens are used to test samples during product development or to produce small pieces on a light workload basis.
- Ovens on conveyor belts
Conveyor ovens are designed to fit into a certain manufacturing process and are used in automated manufacturing.
This oven’s kind and description are determined by how it is used. Curing ovens cause a chemical reaction between powder and metal surfaces. Raw materials are dried in drying ovens. Other ovens clean up impurities, prepare metals for processing, and melt metals together.
Industrial Oven come in a variety of shapes and sizes:
It would be impossible to include all of the many types of these kinds of ovens because new ones are being produced all the time. Specialized ovens are created for a specific manufacturing process. The following is a description of the most popular and common types of ovens available from manufacturers and a short information for you guys that we are one of the leading industrial ovens manufacturers.
Types of Industrial Oven:
1. Electric Ovens for Industry
Electrically heated ovens are low-cost, feature short heat-up periods, and precise temperature settings. They’re great for working with flammable materials or metals like aluminum, which can discolor when heated by gas.
2. Ovens With Direct Gas
Gas industrial ovens are more expensive to manufacture than electric ovens, but they are less expensive to operate because gas is less expensive than electricity. They heat up and maintain temperatures more quickly as compared to electric or infrared ovens, resulting in lower operational costs. Natural or propane gas is used in gas industrial ovens.
Curing steel coatings and assisting in the creation of automobile parts such as brake pads and linings are only a few of their many roles.
3. Ovens used for baking
Baking ovens remove moisture, volatile chemicals, and trapped gases from completed objects’ coatings. The baking practice in powder coating heats the powder to its melting point, allowing it to bond to a metal item.
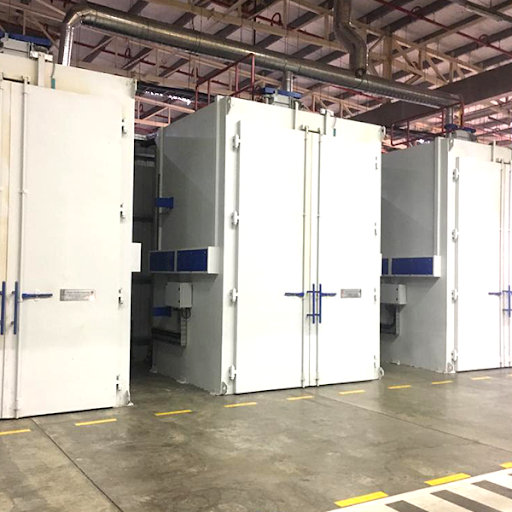
What is the function of Industrial oven?
The kind of fuel used to heat the oven, which can be hot water, direct or indirect gas, ultraviolet light, steam, and electricity, is the first item to consider when describing how an oven works.
The ovens airflow pattern, which may be:
- Horizontal – for objects that are stacked on shelves or hung from the ceiling
- Horizontal/vertical – Air is recirculated through ducts in the ceiling.
- Vertical/Horizontal – The air supply enters through the ceiling and departs through the walls via return ducts.
- Parts are hung or placed on perforated shelves. From the ducts to the return supply, air flows.
- To keep the oven temperature consistent, the airflow must move with few impediments and at a constant velocity.
What are the uses of these ovens?
These ovens are used for a wide range of tasks, from coating microscopic electronic components to baking finish coatings on aeroplane and truck parts. They eliminate moisture in cleanrooms to aid with the removal and containment of pollutants.
These Ovens Have a Variety of Applications
These ovens have a large and diverse list of applications. They’ve become a necessary component of all types of manufacturing in order to increase product performance and reliability. A few of the more common applications are described here.
- Sterilisation
As may be seen in the dry heat steriliser depicted below, these ovens are used to sanitise medical devices and instruments. The eradication of germs, microorganisms, and viruses in the medical industry necessitates equipment with precise temperature control.
- Pharmaceuticals
Coatings on pills are baked in ovens, which also act as an oxidizer to remove excess chemicals and debris from the coatings.
- Sintering
Injection moulding and metallurgy use these ovens to condense and bind materials below their melting point. The sintering process improves the strength and density of a material.
Purchasing Factors:
Evaluate the following assessments:
- Cost
- Maintenance
- Safety
- NFPA Standards for Volatility
- Industrial ovens are extremely productive and useful, but there are a few things to consider before using or purchasing one.
Conclusion
These ovens are used to heat treat parts, metals, and manufacturing components at extremely high temperatures. Drying, curing, testing, and coating are all common uses for industrial ovens. Direct and indirect gas, electricity, ultraviolet rays, and steam are used to heat industrial ovens.
So don’t think much just grab your phone and contact us, we are Maharith Thermal and we are not just oven manufacturers but we are Industrial Furnace Manufacturers also, you can contact us for all types of Furnace. We don’t believe in quality compromise so you can be stress free and believe in our services towards you.